Electro-Kut prend le virage 4.0
C’est en 1986, que Christian Delisle et Ron Fournier se sont associés pour fonder Electro-Kut. Comme l’indique son nom, Electro-Kut a débuté comme spécialiste de l’électroérosion*.
La croissance d’Electro-Kut
Les deux associés avaient choisi d’investir dans l’électroérosion à cause de son potentiel de développement. Mais le financement des machines qui coutaient près de 120 000$ chacune à l’époque était très difficile pour une PME. M. Delisle souligne que l’aide de la Banque de développement du Canada, de Machine Tool Finance Group et de la Banque de Montréal a été cruciale pour le développement de son entreprise. La compagnie a par la suite ajouté des machines-outils utilisant des procédés de fabrication plus traditionnels.
Electro-Kut a toujours œuvré sur des pièces très complexes et demandant une très grande précision. Elle a également développé une expertise en outillage mécanique. Puisque l’usinage dans le secteur aérospatial demande une grande précision, c’est tout naturellement qu’Electro-Kut s’y est intéressée. Malgré sa capacité à produire avec précision, l’obtention des normes de certification en aéronautique a été très exigeant. Entre autre, depuis 2011, Electro-Kut est accréditée NADCAP pour ses procédés EDM. La seule entreprise au Québec a détenir cette accréditation à cette fin.
Le PME lavalloise, qui compte maintenant 65 employés, tire 80% de ses revenus du secteur aérospatial. Ce fournisseur de troisième niveau fait affaire avec les principaux équipementiers de la grappe aérospatiale montréalaise. Ses pièces fabriquées se retrouvent notamment sur des avions d’Airbus, de Boeing ainsi que sur plusieurs avions d’affaires.
Dernièrement, elle a obtenu des mandats de fabrication sur plusieurs programmes d’avions en croissance. M. Delisle prévoit une augmentation du chiffre d’affaires de 30% en à peine 18 mois.
Le financement
Pour une PME, le financement est toujours une question critique quand vient le temps de prendre de l’expansion. 30% de croissance en moins de 24 mois, c’est énorme pour une compagnie de la taille d’Electro-Kut. Au problème de financement il faut ajouter celui de la pénurie de main-d’œuvre.
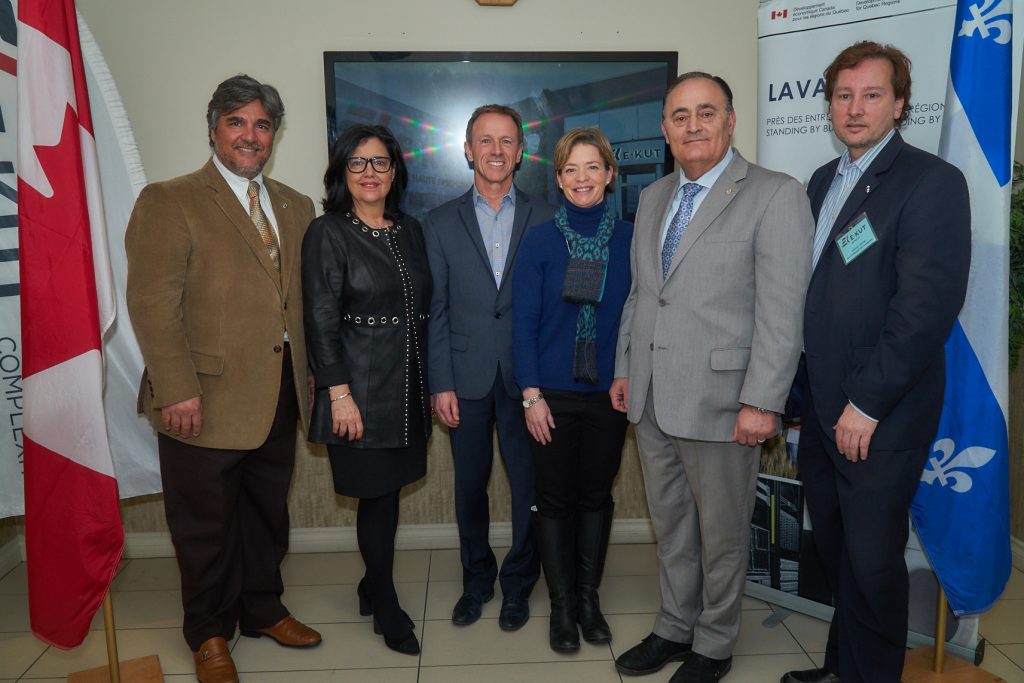
Pour répondre à ses besoins, Electro-Kut a donc choisi de se tourner vers la fabrication 4.0. L’entreprise, investira près de 3 M$ dans l’achat de trois machines-outils semi autonomes afin de porter son chiffre d’affaires à 9 M$. L’annonce faite hier, portait sur un prêt remboursable mais sans intérêts de la part de Développement économique Canada. Sans ce prêt de 825 000 $, Electro-Kut n’aurait pas été en mesure de rencontrer tous ses besoins d’équipement.
Notez qu’Investissement Québec et la BMO participent également au soutien financier d’Electro-Kut.
Une fois rodées, les nouvelles machines ne nécessiteront qu’une seule heure d’intervention humaine par période de 24 heures d’usinage. Les besoins de main d’œuvre supplémentaire seront surtout pour de la programmation. L’objectif d’Electro-Kut avec ces nouvelles machines est d’être en mesure de produire 80% du temps disponible.
*Wikipedia définit l’électroérosion de la manière suivante :
« Ce procédé d’usinage consiste à faire passer un courant dans un diélectrique, afin de générer une « bulle » de vapeur ou de vide qui s’ionise et se résorbe en implosant, entraînant la destruction de la matière. Cette destruction (micro-implosion) provoque l’étincelle. Le courant de forte intensité ionise un canal à travers le diélectrique. Une décharge disruptive se produit alors, de l’électrode vers la pièce à usiner, détériorant celle-ci très localement (quelque µm²). Le diélectrique refroidit alors les particules détériorées, qui tombent dans le bac de la machine sous forme d’une boue (micro particules de matière et diélectrique).
Les vitesses d’usinage ne sont pas très élevées (entre 0,2 et 10 mm/min), mais la précision en est tout à fait l’opposé. Sur une machine bien entretenue, on peut aisément atteindre plus ou moins 5 µm sur la cote désirée.
De l’eau ou une huile diélectrique spéciale est utilisée dans le bac où la pièce usinée est immergée. Elle est continuellement filtrée. Dans le cas de l’eau, elle est aussi dé-ionisée par une résine.
Le procédé est recommandé dans les usinages de matériaux très durs (mais impérativement conducteurs), des aciers trempés, ou encore dans les cas où la complexité de la pièce l’exige.
Il existe trois types d’usinage par électro-érosion :
- l’électroérosion par enfonçage, dans laquelle une électrode de forme complémentaire à la forme à usiner s’enfonce dans la pièce ;
- l’électroérosion par fil, où un fil conducteur animé d’un mouvement plan et angulaire découpe une pièce suivant une surface réglée ;
- le perçage rapide, qui utilise une électrode tubulaire pour percer les matériaux très durs. »