À propos des ailes du C Series et du Global 7500
Au cours des derniers mois, Bombardier a acheté des mains de Triumph l’usine de production des ailes du Global 7500 et mis en vente celle qui fabrique les ailes du C Series à Belfast. Voici notre analyse de ces deux décisions récentes.
Le bijou
Le C series est un des seuls avions de ligne avoir une aile dont la structure et le revêtement sont en composite et cela lui confère une légèreté et une résistance exceptionnelles. De plus son profil aérodynamique offre un des meilleurs (sinon le meilleur) ratio Portance /Trainée de toute l’industrie. La technologie derrière la fabrication de cette aile est un véritable bijou et la décision de Bombardier de se départir de l’usine qui la fabrique en a surpris plus d’un.
Afin de rencontrer les exigences d’Airbus en réduction de coûts, Bombardier aurait été obligé d’investir à nouveau dans son usine de production d’ailes de Belfast afin d’en améliorer la productivité. À court et moyen terme, Bombardier n’aurait pas été en mesure de reprendre son investissement. De plus, la technologie de l’aile du C series est dispendieuse et demande une production élevée afin de pouvoir répartir les coûts sur un grand nombre d’unités, elle ne convient donc pas aux avions d’affaires.
Lorsque Bombardier a lancé la mise au point de la technologie pour les ailes du C Series, plusieurs nouveaux programmes d’avions étaient en développement et rien n’indiquait qu’une dizaine d’années plus tard l’industrie aérospatiale arrêterait pratiquement tout développement de nouveaux programmes d’avions commerciaux. C’est pourtant le cas actuellement et le seul projet encore dans les cartons chez Boeing, vient de prendre le bord avec la crise du MAXGATE.
L’absence de nouveaux programmexx d’avion commerciaux qui auraient permis à Bombardier d’augmenter les revenus de cette usine aura sans doute joué pour beaucoup dans la décision de vendre ce bijou qui a perdu beaucoup de sa valeur.
La perle rare
L’aile du Global 7500 est une autre grande réussite de Bombardier car le défi était de taille; son grand envergure, son poids relativement léger, sa capacité à contenir 25 000 livres de carburant et son ratio Portance/Trainée en fait une aile exceptionnelle. C’est son aile qui a permis au Global 7500 d’atteindre et de surpasser tous les objectifs que Bombardier s’était fixés.
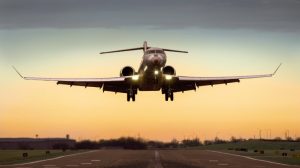
Durant tous les déboires de Triumph avec la fabrication de l’aile du Global 7500, c’est le département d’ingénierie de Bombardier qui a été obligé de résoudre les problèmes un après l’autre. La décision de racheter la production était donc facile à prendre car Bombardier avait perdu toute confiance envers ce fournisseur.
À moyen terme, l’expérience acquise avec l’aile du Global 7500 devrait pouvoir être transférée vers d’autres programmes d’avions d’affaires de Bombardier, ce qui lui confère plus de valeur.
Le joyau
Parler des qualités des ailes conçues par Bombardier sans parler de l’aérodynamicien Fassi Kafyeke serait injuste. M. Kafyeke est entré à l’emploi de Bombardier en tant qu’aérodynamicien en 1982. Il est titulaire d’un diplôme d’ingénieur en aérospatiale de l’université de Liège en Belgique, d’une maîtrise en génie du transport aérien du Cranfield Institute of Technology du Royaume-Uni et d’un doctorat en génie mécanique (Aérodynamique) de l’École Polytechnique de Montréal.

En 2007, il a été promu directeur en charge des technologies stratégies. Depuis 2015, il est le directeur principal en charge des technologies stratégiques et de la conception avancée et membre de l’équipe de direction de l’ingénierie en développement des produits aéronautiques de Bombardier. Il s’occupe également de l’innovation technologique, de l’innovation des produits et de l’écoconception.
M. Kafyeke est très respecté de ses collègues et lorsque l’on mentionne son nom les éloges viennent rapidement. De l’avis de plusieurs chez Bombardier, il est le principal artisan des performances exceptionnelles des ailes du C Series, du Global 7500 et Global 6500 et du Global 5500. M. Kafyeke est un ingénieur de grande valeur pour une entreprise comme Bombardier et c’est pour cette raison que nous lui avons donné le titre de joyau.
Nous complétons ce texte avec une petite devinette :
M. Kafyeke a travaillé sur l’aile du C series dont la masse maximale au décollage est dans les 60 T, puis il a travaillé sur l’aile du Global 7500 avec une masse maximale dans les 50 T, par la suite il s’est attaqué aux ailes du Global 6500 et 5500 dont la masse maximum est dans les 40 T.
Selon vous, le prochain avion sur lequel travaillera M. Kafyeke aura une masse maximale dans les …
>>> Suivez-nous sur Facebook et Twitter
L’A220 n’est pas le seul avion de ligne avec une aile en composites, il y a également les 787 et A350 qui eux ont une aile pratiquement 100% composites ou presque contre peut-être 80-85% pour l’A220 (les nervures (ribs) sont en aluminium).
Correct je corrige, mais tu n’as pas répondu à la question quizz.
Et bien selon moi ce sera pour remplacer le CL650 qui fait 22 tonnes mais devrait y avoir au moins 2 versions dont une qui sera plus grande près de 30 tonnes
L’aile du CSeries a une teneur en fibre de carbone légèrement supérieure à celle du 787 Dreamliner. Ni l’un ni l’autre n’a une aile « pratiquement 100% composite » et il est faux de dire que l’aile du 787 en contient davantage que celle du A220 car l’aile de ce dernier en contient environ 2% de plus.
Cependant le fuselage du CSeries est en aluminium-lithium alors que celui du 787 est presqu’entièrement en carbone. Il aurait donc été plus juste de dire que le 787 est presqu’entièrement en composite alors que l’A220 ne l’est qu’à moitié. Par contre l’aile du A220 contient davantage de CFRP en pourcentage.
Voici quelques extraits d’un article de Leeham News and Analysis concernant l’aile du A220:
The BBD C Series wing is better than Airbus with its A350 wing and Boeing with its 787 and 777X wings, as it’s not using pre-preg tape (tape which has been pre-impregnated with resin), which is then laid down with a tape layer on the female wing skin mold. Pre-impregnated tape has a limited lifetime and needs to be stored cold and is more expensive than its parts: carbon cloth and resin.
Instead, Bombardier lays the dry cloth (cut mats) on the mold, covers the clot layers with a plastic bag so one can apply a vacuum in one end that sucks resin in from the other end, gradually flowing over the cloth and wetting it to a CFRP matrix.
Tape laying introduces pockets of air under the tape. An autoclave with 150 PSI is needed to compact the air bubbles trapped under the tape. If large air bubbles are present in CFRP, it lowers the strength. The fibers can bend in the air bubbles when the CFRP is compressed, resulting in poor strength of the CFRP.
Michael McLean, who has the mouthful title of Director of Operations C Series-Wing Manufacturing/Assembly and Composites, says that the facility has a 99% completion rate. Only 1% of the wings emerge from the autoclave with flaws that must be disposed of.
Bombardier’s method is more advanced than Airbus or Boeing for the A350 and 787.
Sucking resin in over a dry cloth is cheaper and gives better quality (if you do it right). BBD, in addition, uses an autoclave to compact the cloth during the sucking process, giving even higher quality and, most importantly, it reduces the variability of the result.
BBD’s process and experience is simply the next step. If you then can cure the CFRP without pressure, just heat, it’s even better. But it’s difficult; the result is a bit lower quality and a bit higher variability. Mastering this like the Russian Aerocomposite for the Irkut MC-21 is a further step.
Where and when the resin is added to the dry carbon fiber cloth which is laid and bagged on the female wing skin form is key.
The resin is only sucked into the bagged fibers after the whole lot has been placed in the autoclave. This enables the hot autoclave to help with the flow of the resin into the bagged fibers and to wet them well.
The more common way is to suck the resin into the bagged fibers in room temp before putting the lot in the autoclave, as one can then survey how it flows.
But sucking in the resin in the autoclave gives a more homogeneous CFRP.
Michael said Bombardier’s long experience using composites on its corporate and regional jets is why Bombardier is ahead of Airbus and Boeing.
Bombardier has been producing composites for 40 years, or about 1978. Airbus was in its infancy. Boeing was using in the early stages of composite components.
https://leehamnews.com/2018/01/29/bombardiers-belfast-c-series/
QUOTE
Michael McLean, who has the mouthful title of Director of Operations C Series-Wing Manufacturing/Assembly and Composites, says that the facility has a 99% completion rate. Only 1% of the wings emerge from the autoclave with flaws that must be disposed of.
UNQUOTE
Est-ce que ce chiffre de 99% est correct ? Est-ce qu’il y a eu suffisamment d’ailes produites pour pouvoir confirmer ce taux de rebut ?
Si la personne en a parlé c’est qu’il y a probablement un taux de rebut plus élevé que ça, sinon on ne dit tout bêtement rien.
L’injection de résine est bien connue pour être difficilement reproductible. Des fois ça laisse des bulles.
Peut-on investiguer plus à ce sujet de taux de rebut ?
Voici un extrait de Reinforced Plastics:
Most of the CSeries wing, about 80% of it in fact, is composite. Specifically the torque box – the wing’s main strength member – and wing skins are of carbon fibre reinforced plastic (CFRP), as are the moving control surfaces (ailerons, spoilers and flaps). Other CFRP parts include the winglets, fixed trailing edge shrouds and main landing gear doors. However, parts of the internal stiffening structure, notably the ribs, are of aluminium alloy, together with the wing leading edge and slats, while the attachments for the engine pylons are titanium.
http://csmres.co.uk/cs.public.upd/article-downloads/Bombardier-final.pdf